Q: What loads can an air bearing carry?
A: It depends on the size of the bearing. PI’s linear bearings can carry up to 750 kg and rotary bearings can carry up to 490 kg. The larger the bearing, the larger the stiffness and payload capacity.
Q: Can I use an air bearing in vacuum?
A: Generally no. While it is not impossible, it is very difficult and should be avoided.
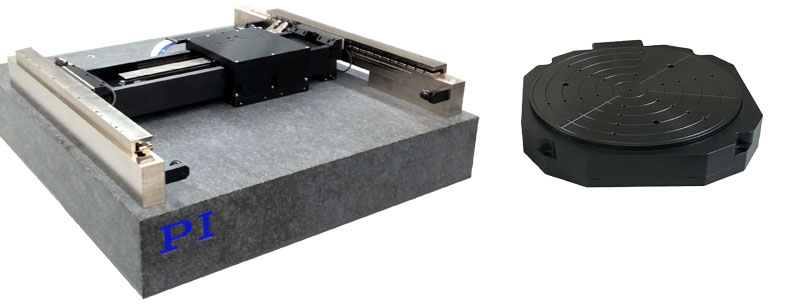
Q: What types of environments can air bearings be used in?
A: Generally clean, dry, and temperature controlled locations. However, PI has built machine tools that use flood coolant with air bearings.
Q: How stiff are air bearings?
A: It depends on the size of the bearing. PI makes large bearings with stiffness above 700 N/µm. In general, an air bearing’s stiffness is very predictable and linear, unlike mechanical bearings. Mechanical bearings are stiffer, but not predictable.
Q: Can you lock down an air bearing?
A: Yes. Most bearing designs will lock down if the air supply is turned off. The locking behavior can be optimized with custom designs. Note: The bearing moves when it locks.
Q: What are typical lead times?
A: 8 weeks for standard products with no motors, 12 weeks for stages with motors, 16-24 weeks for custom designs and systems.
Q: What is the gap (or fly-height) of an air bearing?
A: Typically 10-20 µm.
Q: How fast can air bearings go?
A: Linear bearings are limited to about 5 m/sec, rotary bearings can go up to 1500 RPM. High speed spindles can go 20,000 RPM or more. (PI does not specialize in high speed spindles).
Q: Does PI make porous carbon bearings?
A: No, we only make discreet orifice bearings.
Q: What are some typical air bearing precision specs?
A: Linear: Straightness/Flatness 0.1µm/25mm, Pitch/Yaw 0.5 arc-sec/25mm
Rotary: Radial/Axial Runout 0.1µm, Wobble < 1 arc-sec
Read more >> here
Q: What’s better at making very small steps – an air bearing or a mechanical bearing?
A: For making very small steps (<5 nm), a good cross-roller bearing stage or piezo-flexure stage will outperform an air bearing stage, assuming the same encoder and control system is used. This is due to the damping and friction inherent in the mechanical bearing.
Q: What’s better at scanning performance – an air bearing or a mechanical bearing?
A: An air bearing will almost always outperform a mechanical bearing at scanning, assuming similar encoders and controls. Also, scanning performance of air bearings generally is not affected by speed (very slow or very fast).
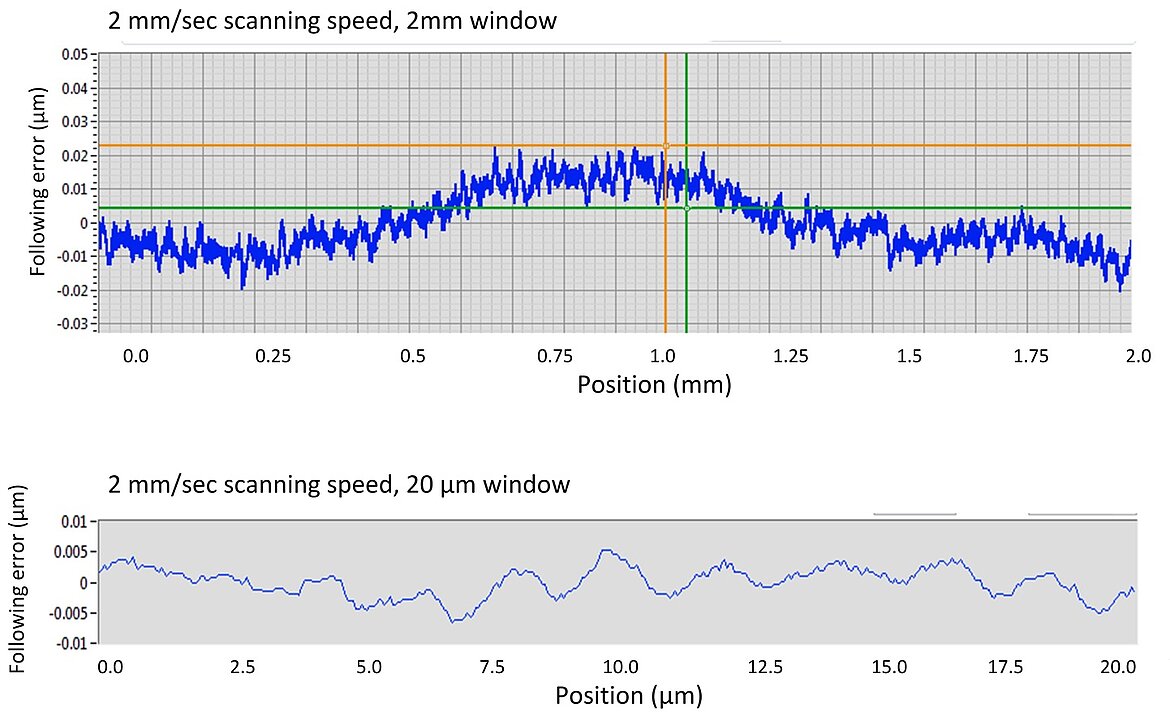
Q: What are air bearings made from?
A: Most common is aluminum with a coating called hard-coat. PI also use stainless steel and nickel plate steel. Granite is often used as the bearing support surface or structure.
Q: What happens if the bearing moves with the air off?
A: Forcing an air bearing to move with no air can damage the bearing, although it will often be ok. The mating surfaces are quite durable, but contaminants can cause scratches.
Q: Do air bearings wear out?
A: The air bearing life is unlimited, assuming the following:
- The bearing is kept clean and the surfaces undamaged
- The air supply is kept clean, dry, and oil-free
As long as nothing damages the bearing it will run forever. The maintenance of the air filters and the air compressor is the important thing. After that, the life-limiting items are usually the flex cables, which will wear out and break after too many cycles (many millions). Motor coils and encoders usually only fail if they have been damaged, or have a short, or overheat.
Q: Can an air bearing stage work in a vertical (lift) application?
A: Yes. The problem with vertical applications is how you support the gravity load. In a typical ballscrew-driven stage, the mechanical advantage of the screw can support the load with minimal load on the motor. However, in a direct-drive system, motors will overhead in this case. The solution is to add a pneumatic counterbalance mechanism to support the gravity load. PI has built many such systems. Counterbalances to add some cost and complexity to the system and require extra space.