Motion hexapod; BLDC motor; absolute encoder; 10 kg payload; 60 mm/s maximum velocity. Connecting cables are not included in the scope of delivery and must be ordered separately.
H-840 Hexapod 6-Axis Positioning System
Precise, Versatile, Fast, Excellent Value
- CIPA certified
- Travel ranges to ±50 mm / ±30°
- Repeatability to ±0.1 µm
- Velocity to 60 mm/s
- Absolute encoder or incremental encoder
- Payload to 30 kg


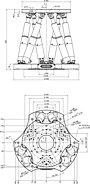












The H-840 hexapod 6-axis precision positioning system provides high resolution motion in 6 degrees of freedom. PI hexapod 6-axis stages are based on the Stewart Platform parallel kinematics principle, with 6 high performance motorized actuators working in parallel between two platforms. H-840 hexapod positioning systems come in different variants, optimized for specific motion and positioning applications. With a precision gear box deployed within each of the six actuators, the H-840.G hexapod models provide higher load capacity and higher resolution. In contrast, the H-840.D models use brushless servo motors to drive the actuators directly, provide higher dynamics and enable velocities to 60 mm/s. For applications that require even higher resolution, the H-840.G2IHP variant with minimum incremental motion to 20 nanometers is offered.
High Performance Parallel-Kinematic Micro Robot Design
H-840 high resolution hexapods are parallel-kinematic positioning systems, widely referred to as parallel kinematic machines or 6-DOF parallel micro robots. The parallel kinematics principle offers extreme versatility and a more compact and stiffer design than conventional, multi-axis positioning systems (serial kinematics or stacked stages).
Why Use Hexapod Positioning Systems?
Hexapod 6-axis positioning and motion systems provide better multi-axis accuracy repeatability than conventional stacked multi-axis stages and support greater motion profile flexibility in a compacter setting. In a stacked 6-axis stage, the bottom stage must carry the load of all 5 axes above while the lightweight moving platform of a hexapod is supported by all 6 actuators in parallel. Due to the significantly reduced moved mass, hexapod positioning systems can provide higher dynamics with a similar performance across all motion axes. Cable management is not an issue for PI H-840 hexapod positioners because all 6 actuators are connected to the stationary base platform. With only two cables to plug into the static hexapod base platform, one for power and one for position information feedback to the hexapod controller, cable management and connectivity are greatly simplified within the local applications. Unlike stacked multi-axis stages, there are no moving cables.Servo controller tuning is also easier to manage since all six hexapod actuators are identical and generally support a similar load. In most hexapod applications, users need not modify the default factory servo parameter settings on the hexapod controller.
Why Use Absolute Encoders in a High Precision Hexapod Positioning System?
H-840 hexapods are available with absolute measuring position encoders. Absolute encoders supply the correct position information to its motion controller immediately after startup, rendering referencing moves unnecessary and thus increasing efficiency and safety in case of a power outage or connectivity loss.
Four Decades of Parallel-Kinematics Motion Systems Design Experience
PI began developing parallel-kinematic nanopositioning systems over 40 years ago and was a pioneer in the early 1990s, introducing motorized, high precision 6-axis hexapod motion and positioning devices for demanding optics and astronomy applications. Today, PI is the world leading supplier of highly accurate parallel kinematic motion systems for sub-micrometer to sub-nanometer ranges, multi-axis positioning, alignment and motion applications.
Superior Mechanical Design
The H-840 mechanics employ cardanic joints with Z-offset for increased stiffness and low-friction, as well as high precision ball screws and high-resolution encoders. With several decades of innovation, our design teams have continuously optimized and refined the mechanical design.
6-Axis Motion Controller / Programming / Software
PI’s highly integrated, C-887 6-axis hexapod controller allows quick and simple operation of the H-840 hexapod systems. The user need not deal with the specific hexapod kinematics as all coordinate transformations are executed internally. As with conventional, stacked multi-axis positioning systems, all positions can be easily addressed using Cartesian coordinates. With the powerful C-887 hexapod controller and PI’s intuitive software packages, users can easily program arbitrary pivot points, a very important feature when creating alignment applications for fibers, optics, lenses or large panels. PI’s C-887 hexapod motion controller supports user-programmable coordinate systems and offers interface options that include EtherCat®, USB, Ethernet and analog inputs.
Brushless Servo Motors (BLDC) for High Duty Cycles
The 6 hexapod actuators are driven by brushless DC servo motors (BLDC). Unlike conventional brushed servo motors, BLDC motors do not generate particles and provide higher torque over a longer lifetime.
Manual 6-Axis Control
PI hexapods can be manually controlled over all 6 degrees of freedom using the C-887.MC2 manual control unit, a great advantage and time saver when setting up an application. This hand-held controller plugs into the hexapod controller and provides six individual knobs, one for each axis (X, Y, Z, Pitch, Yaw, Roll), similar to conventional 6-axis stages. The current position information is shown on an LCD display.
PIVirtualMove / Collision Avoidance Software
The hexapod simulation software simulates the limits of the workspace and payload of a hexapod, allowing users to verify that a specific hexapod model can handle the required loads, forces, and torques that occur in an application. The simulation software tool takes the position and motion of the hexapod into account as well as the pivot point and several reference coordinate systems. The C-887.VM1 software helps users avoid motion profiles that would cause the hexapod or assemblies mounted on the hexapod to collide with objects in the vicinity.
Smaller and Larger Hexapods, High Speed Hexapods
The H-840 six axis system is a mid-size hexapod for medium loads. With a wide range of standard hexapod models and multiple configuration options, PI offers the largest range of precision positioning hexapods: from palm-sized-devices such as the H-811 to large units with hundreds of kilograms of load capacity. PI hexapods are used in all kinds of applications, from micro-lens and fiber-alignment, machining and automated assembly of complex parts, and automotive to aerospace. A special voice-coil actuator hexapod is available for high precision, high-velocity motion simulation. When nanometer and sub-nanometer precision and millisecond responsiveness are required, PI offers piezo-based multi-axis nanopositioning systems, such as the PIMars 6DoF stage family.
Hexapod Applications: What Are Hexapods Used For?
H-840 hexapod 6-axis positioning systems are deployed in a wide range of industrial, automation and research applications, including micromanufacturing, micromanipulation, fiber alignment, automated optical and mechanical alignment, satellite sensor testing, optical metrology, tool inspection, X-ray diffraction, beamline sample positioning, and life sciences. The direct-drive high-speed version of the H-840 is CIPA certified for motion simulation, critical for imaging sensors and camera quality test.
Specifications
Specifications
Motion | H-840.D2A | H-840.D2I | H-840.G2A | H-840.G2I | Tolerance |
---|---|---|---|---|---|
Active axes | X ǀ Y ǀ Z ǀ θX ǀ θY ǀ θZ | X ǀ Y ǀ Z ǀ θX ǀ θY ǀ θZ | X ǀ Y ǀ Z ǀ θX ǀ θY ǀ θZ | X ǀ Y ǀ Z ǀ θX ǀ θY ǀ θZ | |
Travel range in X | ± 50 mm | ± 50 mm | ± 50 mm | ± 50 mm | |
Travel range in Y | ± 50 mm | ± 50 mm | ± 50 mm | ± 50 mm | |
Travel range in Z | ± 25 mm | ± 25 mm | ± 25 mm | ± 25 mm | |
Rotation range in θX | ± 15 ° | ± 15 ° | ± 15 ° | ± 15 ° | |
Rotation range in θY | ± 15 ° | ± 15 ° | ± 15 ° | ± 15 ° | |
Rotation range in θZ | ± 30 ° | ± 30 ° | ± 30 ° | ± 30 ° | |
Maximum velocity in X | 60 mm/s | 60 mm/s | 2.5 mm/s | 2.5 mm/s | |
Recommended velocity in X | 40 mm/s | 40 mm/s | 2 mm/s | 2 mm/s | |
Maximum velocity in Y | 60 mm/s | 60 mm/s | 2.5 mm/s | 2.5 mm/s | |
Recommended velocity in Y | 40 mm/s | 40 mm/s | 2 mm/s | 2 mm/s | |
Maximum velocity in Z | 60 mm/s | 60 mm/s | 2.5 mm/s | 2.5 mm/s | |
Recommended velocity in Z | 40 mm/s | 40 mm/s | 2 mm/s | 2 mm/s | |
Maximum angular velocity in θX | 700 mrad/s | 700 mrad/s | 30 mrad/s | 30 mrad/s | |
Recommended angular velocity in θX | 480 mrad/s | 480 mrad/s | 25 mrad/s | 25 mrad/s | |
Maximum angular velocity in θY | 700 mrad/s | 700 mrad/s | 30 mrad/s | 30 mrad/s | |
Recommended angular velocity in θY | 480 mrad/s | 480 mrad/s | 25 mrad/s | 25 mrad/s | |
Maximum angular velocity in θZ | 700 mrad/s | 700 mrad/s | 30 mrad/s | 30 mrad/s | |
Recommended angular velocity in θZ | 480 mrad/s | 480 mrad/s | 25 mrad/s | 25 mrad/s | |
Amplitude-frequency product in X | 23.6 mm·Hz | 23.6 mm·Hz | — | — | |
Amplitude-frequency product in Y | 23.6 mm·Hz | 23.6 mm·Hz | — | — | |
Amplitude-frequency product in Z | 8 mm·Hz | 8 mm·Hz | — | — | |
Amplitude-frequency product in θX | 5.1 °·Hz | 5.1 °·Hz | — | — | |
Amplitude-frequency product in θY | 5.1 °·Hz | 5.1 °·Hz | — | — | |
Amplitude-frequency product in θZ | 14 °·Hz | 14 °·Hz | — | — | |
Amplitude-frequency² product in X | 65.9 mm·Hz² | 65.9 mm·Hz² | — | — | |
Amplitude-frequency² product in Y | 65.9 mm·Hz² | 65.9 mm·Hz² | — | — | |
Amplitude-frequency² product in Z | 22.5 mm·Hz² | 22.5 mm·Hz² | — | — | |
Amplitude-frequency² product in θX | 14.7 °·Hz² | 14.7 °·Hz² | — | — | |
Amplitude-frequency² product in θY | 14.7 °·Hz² | 14.7 °·Hz² | — | — | |
Amplitude-frequency² product in θZ | 41 °·Hz² | 41 °·Hz² | — | — | |
Amplitude error | 10 % | 10 % | — | — | max. |
Phase error | 60 ° | 60 ° | — | — | max. |
Maximum frequency | 30 Hz | 30 Hz | — | — | |
Positioning | H-840.D2A | H-840.D2I | H-840.G2A | H-840.G2I | Tolerance |
Minimum incremental motion in X | 1.5 µm | 0.5 µm | 0.3 µm | 0.25 µm | typ. |
Minimum incremental motion in Y | 1.5 µm | 0.5 µm | 0.3 µm | 0.25 µm | typ. |
Minimum incremental motion in Z | 1 µm | 0.25 µm | 0.2 µm | 0.15 µm | typ. |
Minimum incremental motion in θX | 10 µrad | 3 µrad | 2 µrad | 2 µrad | typ. |
Minimum incremental motion in θY | 10 µrad | 3 µrad | 2 µrad | 2 µrad | typ. |
Minimum incremental motion in θZ | 2 µrad | 5 µrad | 4 µrad | 4 µrad | typ. |
Unidirectional repeatability in X | ± 0.3 µm | ± 0.3 µm | ± 0.3 µm | ± 0.3 µm | typ. |
Unidirectional repeatability in Y | ± 0.3 µm | ± 0.3 µm | ± 0.3 µm | ± 0.3 µm | typ. |
Unidirectional repeatability in Z | ± 0.1 µm | ± 0.1 µm | ± 0.1 µm | ± 0.1 µm | typ. |
Unidirectional repeatability in θX | ± 1.5 µrad | ± 1.5 µrad | ± 2.5 µrad | ± 2.5 µrad | typ. |
Unidirectional repeatability in θY | ± 1.5 µrad | ± 1.5 µrad | ± 2.5 µrad | ± 2.5 µrad | typ. |
Unidirectional repeatability in θZ | ± 3 µrad | ± 3 µrad | ± 3 µrad | ± 3 µrad | typ. |
Backlash in X | 1.5 µm | 1.5 µm | 2 µm | 2 µm | typ. |
Backlash in Y | 1.5 µm | 1.5 µm | 2 µm | 2 µm | typ. |
Backlash in Z | 0.2 µm | 0.25 µm | 0.3 µm | 0.3 µm | typ. |
Backlash in θX | 4 µrad | 4 µrad | 5 µrad | 5 µrad | typ. |
Backlash in θY | 4 µrad | 4 µrad | 5 µrad | 5 µrad | typ. |
Backlash in θZ | 8 µrad | 8 µrad | 10 µrad | 10 µrad | typ. |
Integrated sensor | Absolute rotary encoder, multi-turn | Incremental rotary encoder | Absolute rotary encoder, multi-turn | Incremental rotary encoder | |
Drive Properties | H-840.D2A | H-840.D2I | H-840.G2A | H-840.G2I | Tolerance |
Drive type | Brushless DC motor | Brushless DC motor | Brushless DC gear motor | Brushless DC gear motor | |
Mechanical Properties | H-840.D2A | H-840.D2I | H-840.G2A | H-840.G2I | Tolerance |
Maximum load capacity, base plate in any orientation | 3 kg | 3 kg | 10 kg | 10 kg | |
Maximum load capacity, base plate horizontal | 10 kg | 10 kg | 30 kg | 30 kg | |
Maximum holding force, base plate in any orientation | 5 N | 5 N | 25 N | 25 N | |
Maximum holding force, base plate horizontal | 15 N | 15 N | 100 N | 100 N | |
Overall mass | 12 kg | 12 kg | 12 kg | 12 kg | |
Material | Aluminum, steel | Aluminum, steel | Aluminum, steel | Aluminum, steel | |
Miscellaneous | H-840.D2A | H-840.D2I | H-840.G2A | H-840.G2I | Tolerance |
Operating temperature range | -10 to 50 °C | -10 to 50 °C | -10 to 50 °C | -10 to 50 °C | |
Connector for data transmission | HD D-sub 78 (m) | HD D-sub 78 (m) | HD D-sub 78 (m) | HD D-sub 78 (m) | |
Connector for supply voltage | M12 4-pole (m) | M12 4-pole (m) | M12 4-pole (m) | M12 4-pole (m) | |
Recommended controllers/drivers | C-887.5xx | C-887.5xx | C-887.5xx | C-887.5xx |
Connecting cables are not included in the scope of delivery and must be ordered separately.
Ask about customized versions.
When measuring position specifications, typical velocity is used. The data is included in the delivery of the product in the form of a measurement report and is stored at PI.
The maximum travel ranges of the individual coordinates (X, Y, Z, θX, θY, θZ) are interdependent. The data for each axis shows its maximum travel range when all other axes are in the zero position of the nominal travel range and the default coordinate system is in use, or rather when the pivot point is set to 0,0,0.
At PI, technical data is specified at 22 ±3 °C. Unless otherwise stated, the values are for unloaded conditions. Some properties are interdependent. The designation "typ." indicates a statistical average for a property; it does not indicate a guaranteed value for every product supplied. During the final inspection of a product, only selected properties are analyzed, not all. Please note that some product characteristics may deteriorate with increasing operating time.
Downloads
Product Note
Product Change Notification Hexapod Cables
Product Change Notification Motor Driven Products
Product Change Notification H-840.D2, H-840.G2
Product Change Notification H-206.x1x, H-8xx.x1x, H-8xx.xVx, F-206.S
Datasheet
Documentation
User Manual MS201
H-840 Hexapod Microrobot
PI Certificate of Registration of Vibratory Apparatus H-840
Certificate of Registration of Vibratory Apparatus
3D Models
H-840.x2x 3-D model
Software Files
PIVirtualMove
Ask for a free quote on quantities required, prices, and lead times or describe your desired modification.
Motion hexapod; BLDC motor; incremental rotary encoder; 10 kg payload; 60 mm/s maximum velocity. Connecting cables are not included in the scope of delivery and must be ordered separately.
Precision hexapod; brushless DC gear motor; absolute encoder; 30 kg payload; 2.5 mm/s maximum velocity. Connecting cables are not included in the scope of delivery and must be ordered separately.
Precision hexapod; brushless DC gear motor; incremental rotary encoder; 30 kg payload; 2.5 mm/s maximum velocity. Connecting cables are not included in the scope of delivery and must be ordered separately.
How to Get a Quote
Ask an engineer!
Quickly receive an answer to your question by email or phone from a local PI sales engineer.
Applications
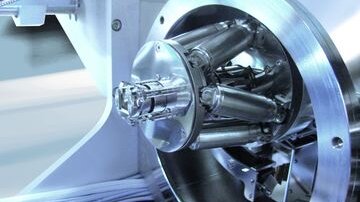
High Vacuum Positioning
Investigation of the structural properties of thin films under high-vacuum conditions.
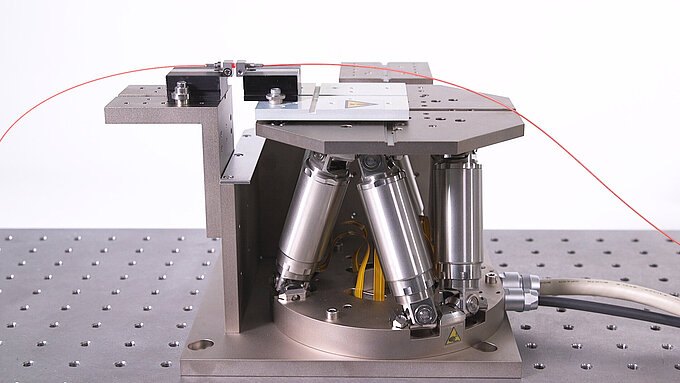
Hexapods in Microproduction
What do optical components and glass fibers in photonics, mobile devices, and high-quality wristwatches all have in common?
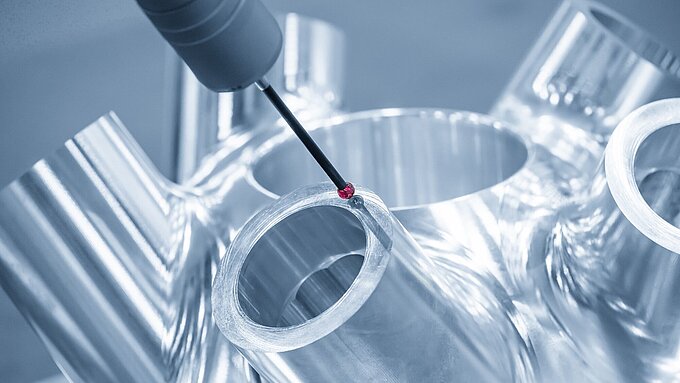
Dimensional Measuring
Hexapods allow for an outstanding flexibility for a variety of samples of in-line automation systems by minimizing the space for motion robotics.